5 Most Common Forklift Accidents and How to Prevent Them
Forklifts are essential tools in warehouses, construction sites, manufacturing plants and other industrial facilities. Their ability to move heavy loads efficiently makes them essential to productivity, but this power also carries significant safety risks. Every year, thousands of accidents involving forklifts result in injuries, property damage and even fatalities.
In this article, we’ll walk you through the five most common forklift accidents, explore what causes them, and offer practical strategies—both human and technological—to prevent them.
Forklift Accident Statistics
Forklift accidents remain a significant concern in industrial and warehouse environments, underscoring the need for stringent safety measures. According to the U.S. Bureau of Labor Statistics (BLS), there were 5,283 fatal work injuries recorded in the United States in 2023. While this figure encompasses all types of workplace fatalities, a notable portion is attributed to incidents involving forklifts and other industrial vehicles.
Additionally, the BLS reported 2.6 million nonfatal injury and illness cases in private industry for the same year, highlighting the broader context of workplace safety challenges.
Forklift-related incidents not only pose a human risk but also carry significant financial consequences. According to the National Safety Council (NSC), the average cost of a workplace injury involving a forklift can exceed $40,000 when considering medical expenses, downtime, equipment repairs, and legal liabilities.
In addition, OSHA estimates that businesses spend millions each year on compensation claims and regulatory fines due to non-compliance. These figures reinforce the need for proactive investment in safety training, monitoring technologies, and operational best practices to prevent accidents before they occur.
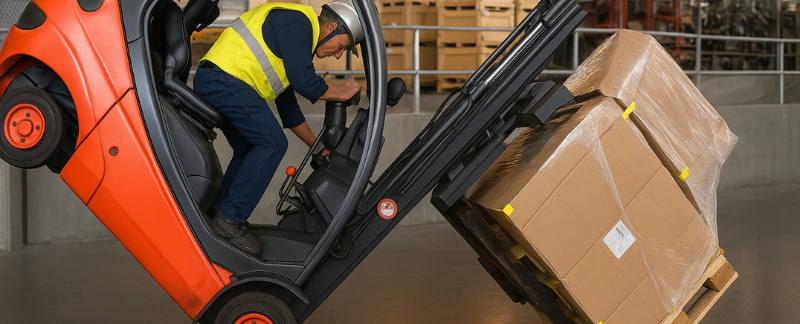
1. Forklift Rollovers
Forklift rollovers are among the most dangerous and fatal types of accidents in material handling environments. These typically occur when the forklift becomes unbalanced, often due to:
- Sharp turns taken at high speeds
- Lifting or carrying loads beyond capacity
- Operating on uneven, rough or sloped surfaces
- Driving with elevated loads
Prevention tips: Operators should follow strict load-handling procedures, always drive with loads close to the ground, and avoid sudden movements. Forklift speed must be appropriate to the environment, especially on slopes and curves. In high-risk areas, advanced forklifts equipped with smart stability sensors, tilt sensors or AI-based monitoring systems can warn operators before rollover scenarios occur, providing a valuable layer of protection.
2. Collisions with Pedestrians
When forklifts and pedestrians share the same space, the potential for disaster rises significantly. Pedestrian impacts are especially common in warehouses, factories and logistic centers where traffic is high. These accidents often occur due to:
- Poor visibility
- Blind spots
- Operator distraction
- Lack of clear safety zones
- Lack of designated pedestrian walkways
Prevention tips: Workplaces must establish a clear separation between pedestrian and vehicle lanes through floor markings, safety barriers and traffic mirrors to enhance visibility. Additionally, AI-powered pedestrian detection systems, can detect pedestrians and trigger real-time alerts for the operator when someone steps into a danger zone, even in complex environments. It dramatically reduces the risk of impact.
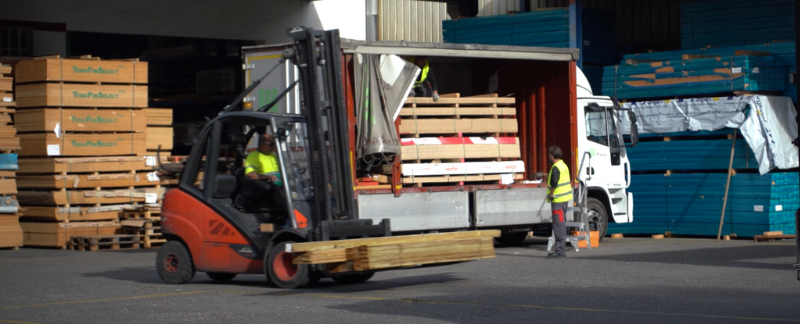
3. Loads Falling from Forks
Poorly secured or improperly balanced loads can fall from elevated forks, potentially crushing pedestrians. This risk increases with high stacking, irregular pallets, or uneven surfaces, and is more common during fast-paced operations with limited visibility. This can cause serious injuries to bystanders, lead to product loss and damage to equipment.
Prevention tips: Forklift operators should ensure that loads are properly secured, evenly distributed, and within the machine’s lifting capacity. They should avoid lifting while moving and only travel with the forks at ground level. AI-powered systems, load stability sensors and mast behavior monitoring can alert the operator if a load is at risk of tipping or slipping.
4. Lack of Operator Training
Untrained or inadequately trained operators are a leading cause of forklift accidents. Without the proper knowledge of machine handling, weight limits, essential safety precautions or hazard recognition, mistakes are inevitable and often costly.
Prevention tips: OSHA-compliant training and certification are non-negotiable. Refresher courses should be held regularly to account for new equipment, updated protocols, or staff turnover. Organizations can further enhance training programs by integrating AI-based safety data to tailor sessions around real-world risks and near-misses.
5. Forklift Tip-Overs at Loading Docks
Loading docks are high-risk areas for forklifts. Accidents are a frequent and often overlooked issue. Forklifts may fall off dock edges or off unstable trailers due to lack of wheel chocks or poor communication between drivers and operators.
Prevention tips: Ensure dock plates are secured, truck trailers are immobilized, and operators confirm readiness before entering. Safety sensors and visual warning systems can alert drivers to high-risk activity near dock edges.
Before loading or unloading, workers must ensure that:
- Dock plates are properly positioned and adequate for weight
- Trailer wheels are chocked
- Communication is established between the dock crew and the truck driver
- Forklifts approach docks slowly and with heightened caution
Visual warning systems, dock edge sensors, and audible alarms can further enhance safety, providing instant alerts in case of hazardous conditions near dock edges.
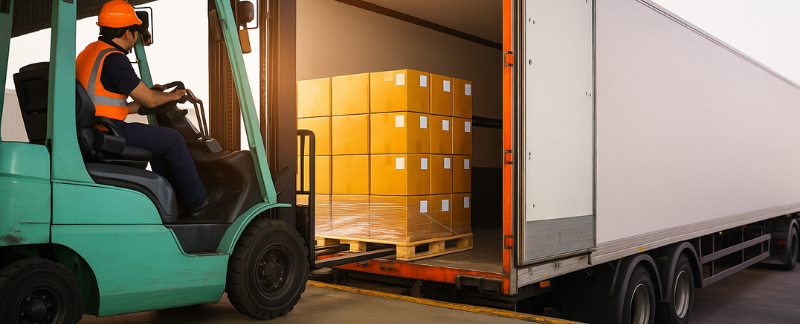
Moving Beyond the Basics: The Role of Smart Safety Technology
Traditional safety measures, such as operator training, hazard signage and equipment maintenance are fundamental. However, they are no longer sufficient on their own. Technology is reshaping how workplaces prevent accidents. It goes beyond reactive protection and enables proactive accident prevention.
AI-based collision avoidance systems now offer real-time pedestrian detection, automatic risk alerts, and even predictive analytics. These solutions are especially effective in environments where human oversight alone is insufficient—such as crowded warehouses or rugged quarry sites.
By combining human vigilance with smart machines, companies can dramatically reduce forklift-related incidents, improve operational efficiency, and create a culture of safety that lasts.
Final Thoughts
Forklift accidents are preventable. With the right mix of training, awareness, environmental design, and intelligent safety systems, your workplace can significantly lower the risk of injury or downtime. Whether you’re managing a warehouse, a mining site, or a public works facility, understanding these common accidents—and how to avoid them—is the first step toward safer operations.
But safety is more than compliance—it’s a driver of performance. Investing in modern safety technologies not only protects workers but also reduces insurance premiums, improves productivity, and enhances a company’s reputation as a responsible employer. In competitive markets, a proactive approach to safety can become a true differentiator.
Ultimately, preventing forklift accidents isn’t just about avoiding harm—it’s about building a culture where safety, efficiency, and innovation go hand in hand. The sooner organizations embrace this mindset, the sooner they’ll reap the benefits across their entire operation.