10 Essential Forklift Safety Tips
Why Forklift Safety Matters
Forklifts play a crucial role in warehouse and industrial environments, but they also pose significant risks when not operated safely. According to OSHA, nearly 100,000 forklift-related accidents occur each year in the United States, with 35,000 resulting in serious injuries and an average of 87 fatalities per year. 11% of forklifts are involved in an accident each year, a rate higher than the automotive industry!
The most common causes include operator error, lack of visibility due to blind spots, mechanical failure, and unsafe warehouse conditions. Prioritizing forklift safety is essential to preventing workplace injuries, reducing costs, and ensuring compliance with safety regulations.
Beyond personal injuries, forklift accidents can cause extensive property damage, leading to costly repairs and operational downtime. Implementing a comprehensive safety program minimizes these risks and fosters a culture of accountability in the workplace. Organizations that take proactive steps toward safety training and technology adoption often see a significant reduction in workplace incidents.
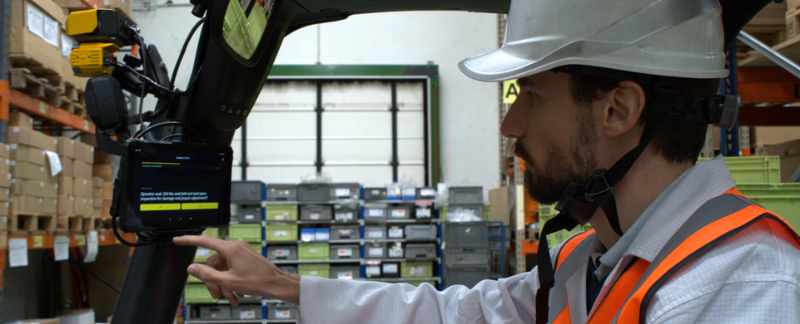
Common Forklift Safety Hazards
Operator Error
Lack of proper training, distractions, and fatigue are the leading factors contributing to forklift accidents. Ensuring that operators are fully certified and participate in ongoing training programs significantly reduces risks. OSHA requires that forklift operators complete training courses and be periodically evaluated to maintain their certification. In addition, employers should reinforce best practices through safety meetings and hands-on refresher courses.
Poor Maintenance and Equipment Failure
Routine maintenance is essential to prevent mechanical breakdowns that could lead to accidents. Forklifts should be inspected daily before use, with checks on brakes, tires, forks, hydraulic systems, and warning signals. A proactive maintenance program ensures that potential issues are addressed before they become safety hazards. Unexpected breakdowns not only compromise safety, but can also disrupt productivity, making scheduled inspections a necessary part of operational efficiency.
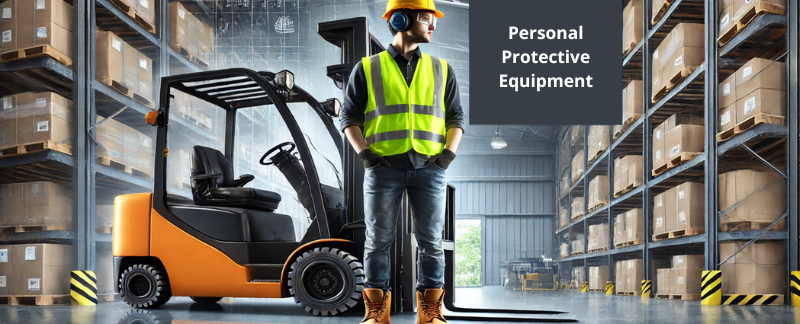
Unsafe Warehouse Design
Poor warehouse layout can contribute to accidents. Narrow aisles, poor visibility, and lack of adequate signage increase the risk of collisions. Warehouse managers should implement clear markings for forklift paths, pedestrian areas, and designated loading/unloading areas to improve safety. Providing proper lighting also improves visibility and reduces the likelihood of accidents occurring due to blind spots.
Essential Tips for Forklift Safety
1. Conduct Regular Safety Training
Ongoing training is vital for maintaining safety standards. Training should cover OSHA regulations, forklift best practices, and emergency procedures. Employees should take refresher courses to stay up-to-date on new safety protocols. Regular assessments ensure that operators remain competent and adhere to safety procedures, reinforcing a strong safety culture within the organization.
2. Perform Pre-Operational Inspections
Before using a forklift, operators should complete a safety checklist, including checking fluid levels, brakes, tires, steering, and warning lights. Identifying potential issues before use prevents mechanical breakdowns. Keeping a record of inspections helps track maintenance needs and ensure compliance with safety regulations.
3. Maintain Clear and Organized Workspaces
Keeping the warehouse free of debris and obstructions reduces the risk of forklift accidents. Designated pathways and properly stored materials help maintain a safe environment. Workspaces should be assessed periodically to ensure continued compliance with safety standards, and any identified hazards should be addressed immediately.
4. Use Proper Load Handling Techniques
Operators should be trained in weight limits, load distribution, and safe lifting techniques. Overloading or improperly balancing the load increases the risk of tipping and falling loads. Forklifts should only carry loads within their rated capacity, and operators should always ensure the load is stable before moving it.
5. Implement Speed and Traffic Controls
Establishing speed limits and respecting forklift lanes helps prevent collisions. Warehouses should use warning signs and floor markings to guide both operators and pedestrians safely. Speed governors can also be installed on forklifts to prevent excessive speeding, further improving workplace safety.
6. Ensure Proper Visibility and Communication
Operators should always have a clear line of sight and use warning signals to communicate their movements. Two-way radios and hand signals also improve communication in noisy environments. When visibility is compromised, such as in blind spots or congested areas, having a spotter can add an extra layer of safety.
7. Wear Appropriate Personal Protective Equipment (PPE)
High-visibility vests, safety helmets, and steel-toed shoes provide essential protection. Employers should enforce the use of PPE as part of their safety policies. Gloves, eye protection, and hearing protection may also be required depending on the work environment.
8. Avoid Forklift Overloading
Exceeding a forklift’s load capacity increases the risk of tipping. Operators should check load limits and distribute weight evenly to ensure stability. Overloading also causes excessive wear and tear on forklift’s components, leading to increased maintenance costs and the risk of unexpected breakdowns.
9. Leverage Advanced Safety Technologies
Modern safety solutions like proximity sensors, automatic speed limitation, and AI detection systems such as Blaxtair improve forklift safety. These technologies help detect pedestrians and specific obstacles and prevent collisions. AI-driven systems can provide real-time alerts to both operators and pedestrians, reducing reaction times and preventing accidents.
10. Follow OSHA Compliance Regulations
Compliance with OSHA regulations is critical for both legal and safety reasons. Companies should stay updated on workplace safety laws and conduct regular safety audits to ensure compliance with these laws. Failure to comply with OSHA standards can result in hefty fines and increased liability, making regulatory compliance a top priority.
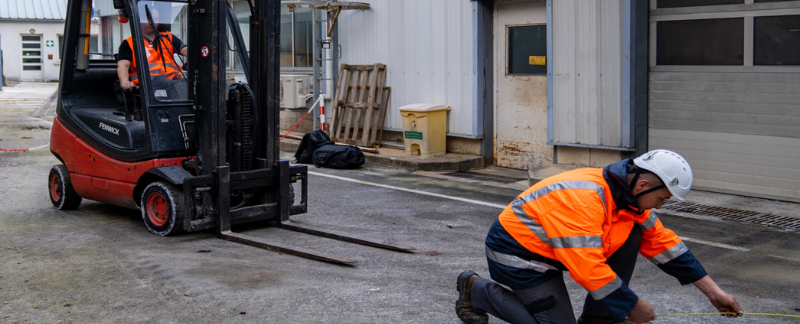
Case Studies on Improved Forklift Safety
Blaxtair helps many companies improve workplace safety and productivity with revolutionary solutions:
- ‘Blaxtair Pedestrian Detection’ is a driver assistance system that improves pedestrian safety. It’s the only industrial-grade AI camera able to detect and localize pedestrians in any posture (i.e standing, crouching, or in partial view) to prevent collisions with forklifts, whether driving forward or in reverse. It prevents accidents by instantly alerting drivers to the presence of a person near the forklift truck without unnecessary alarms. Workers operating on foot therefore remain safe. Drivers can work serenely and focus on their productive task. This reduces their stress. It also helps HSE and site managers monitor and reduce accident risk by a factor of 3.
- ‘Blaxtair OSHA Checklist’ ensures each vehicle is ready to go with a thorough and efficient safety inspection. It provides total peace of mind to operators and their employers as the forklift won’t start if a critical safety question is not answered correctly. Maintenance operators are quickly alerted to fleet status to minimize repair time & unplanned downtime. Fully compliant with OSHA regulations, it enhances workplace safety and operational efficiency.
- ‘Blaxtair Zoning’ provides automatic speed limitation of forklifts in high-risk areas (forklift / pedestrian co-activity, narrow aisles, dangerous intersections etc.). It doesn’t require any heavy radiofrequency-based infrastructure. It significantly reduces accident risks and increases efficiency by eliminating the need for drivers to suddenly stop and restart their vehicles.
These real-world examples demonstrate the tangible benefits of integrating AI-powered safety solutions into daily operations.
Conclusion
Forklift safety should be a top priority for every organization. By implementing these ten essential tips, businesses can create a safer workplace, reduce operational risks, and comply with safety regulations. Organizations that invest in training, technology, and proper maintenance can significantly reduce accidents and ensure a safe work environment for all employees.
For more information on how Blaxtair’s advanced AI solutions can help improve forklift safety and save lives in your facility, visit our Solutions.